空気輸送搬送装置 技術情報
空気輸送搬送とは
輸送方式に関して
輸送方式を方法によって分類すると下図のようになります。
すなわちコンベヤのはこび方に、ベルトコンベヤのように乗せてはこぶ方式、スクリューコンベヤやスクレーパーコンベヤのように押してはこぶ方式,フローコンベヤのように粒間の摩擦力を利用する方式、あるいは空気コンベヤのように風力を使用する方式など、いろいろな方式があります。
一般にこれらいずれの方式をもってしても運部ことの出来るものであれば、その形式の選定は輸送距離、輸送量、占有空間、消費動力および設備費などによって定まります。
輸送方式の分類表
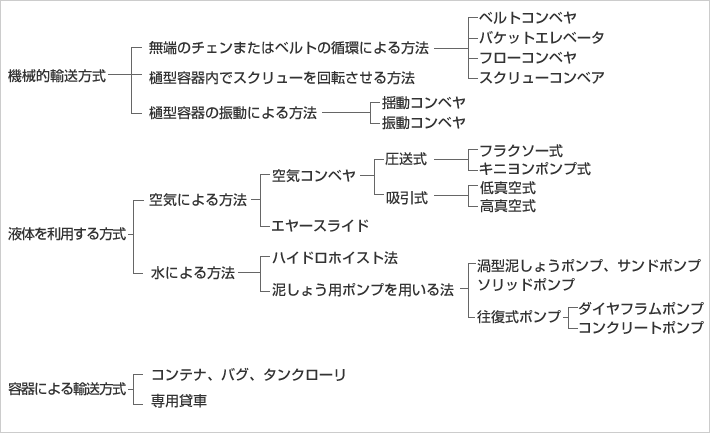
空気輸送搬送機の設計要領とは
空気輸送搬送機の設計に当っては、"適正な配管設計を行なう"の一言につきます。
空気輸送搬送機の最大の長所は、簡単な配管1つを自在に引き回すのみでその目的が達せらる簡便さ、それがプラントに使用されていればそのプラントの機器が任意にその配置を可能にするところにあります。
空気輸送搬送機の最大の主役はその構造の簡単なパイプなのです。
その簡単な配管であるだけに、配管の設計の巧拙が装置全体に及ぼす影響は、非常に多きことが特徴です。
配管が主役であるならば、脇役の役目も重要です。
すなわち、空気ポンプ(圧縮機または真空ポンプ),混入器(ノズル,ロータリーバルブ),分離器の設計もおろそかにはできません。
"適正な配管設計"とは適正な管内流速、混合比を選定して経済的な管径と空気ポンプ動力を決定することにあります。
輸送方式の決定
圧送、真空式どちらを採用するかはその使用目的により必然的に決まってしまう場合もあるものの、様々な条件を考慮してもその方式を決めきれない場合は、そのそれぞれの利点の一番多い方にて決定すべきです。
1. 圧送式
- 1ヵ所から投入して数ヵ所に分散輸送を行なう場合
- 大容量・長距離輸送を行なう場合
- 分離操作の困難な粉休輸送を行なう場合
- 管外よりの異物混入をきらう場合
2. 真空式
- 数ヵ所からlヵ所への集約輸送を行なう場合
- 短距離輸送を行なう場合
- 山積みされた粉体を荷役する場合
- 輸送元で被輸送物の飛散をとくに避けたい場合
上記の目安により輸送方法を決定したら、つぎにそのそれぞれの方法に応した機器(空気ポンプ、混入機、輸送管、分離器)の選定をする必要があります。
たとえばそこで採用される空気ポンプで作られる圧力、または真空に耐える輸送管、混合器の設計が必要になります。
輸送管についてはその強度、被輸送物による摩耗の問題が主ですが、混合器についてはその装置に必要な圧力または真空度を破ることなく、その圧力差のあるところに所定量の輸送物を供給しなければなりません。
また分離器については、その輸送物の種類によっては相当高度の集塵装置の知識を要求されます。
空気輸送搬送機で用いられる集塵機は大体限定され、サイクロン、バグフイルタ程度で、空気集塵器まで持込むことはないですが、湿式集塵器の必要があったり、バグフイルタのろ布の選定には注意を要することがあります。
空気輸送搬送機における配管設計要領まとめ
- 配管による圧力損失を小さくし、動力を節減するため,管内はできるだけ滑らかにし、最短距離の配管になるように心がけてください。
また、ベンドの数はできるだけ減らし,適正な曲率半径をもたせるようにしてください。 - 高い混合比を採用する場合、また硬い輪送物を扱うときは,とくに摩耗を考慮し、管の厚みは十分にとり、摩耗のはなはだしい場所はその一部分、または全体を容易に交換できる構造にしておいてください。
- 錆の混入を避けたい輸送物の場合には、ステンレス鋼、アルミニウム、または塩化ビニールパイプを用いてください。
また、ゴム管や塩化ビニールパイプを使用した際に生ずる静電気に対して、その防止策や安全策は忘れずにとってください。 - 配管の支持はその自重と輸送物充満時の全重量に耐え、さらに配管施工上交換のきかないような個所は摩耗損傷による欠損まで考慮して十分強固なものを用意してください。 また地中埋没管は避けるようにしてください。
空気輸送搬送装置の型式と選定
概要
産業分野に関係なく、粉粒体状の物質を取扱うケースがあります。
すなわち、原料や製品を粉末や粒子の状態で受入れ、これらに精練、反応、混合、分離、乾燥、冷却などの物理、化学的操作を加えて最終製品として、ばら積みあるいは包装して搬出することが多いものです。
これらの製造工程で粉粒体を輸送する方法にはコンテナ、ベルトコンベヤ、チェンコンベヤ、バケットエレベータなどの機械的輸送と、空気で運搬輸送する方法、すなわち空気輸送搬送とがあります。
また特殊な方面では水で輸送する液体輸送も行なわれています。
粉粒体を扱う設備の計画にあたっては、設備の各機器が適確にそれぞれの目的とする機能をはたすとともに、設備全体が合理的に所期の生産目標を達成するように各機器の種類と容量を選定し、同時に全体の配置と操業の計画をたてなければならなりません。
取扱う粉粒体の特性と容量、輸送距離、前後段の状況などと各輸送装置の特性を勘案して、もっともこのましい輸送装置の種類と容量、ならびに付帯設備を選定する必要があります。
空気輸送搬送装置と他の機械的輸送装置との特長の比較
項目 | 空気輸送 | ベルトコンベヤ | チェンコンベヤ | スクリューコンベヤ | バケットエレベータ |
---|---|---|---|---|---|
輸送物飛散 | なし | おそれあり | おそれあり | おそれあり | おそれあり |
異物の混入、汚損 | なし | おそれあり | なし | なし | なし |
輸送物の残留 | なし | なし | あり | あり | あり |
輸送経路 | 自由 | 直線的 | 直線的 | 直線的 | 直線的 |
分岐 | 自由 | 困難 | 困難 | 困難 | 不可 |
傾斜、鉛直輸送 | 自由 | 傾斜に制限 | 構造複雑 | 可能 | 可能 |
輸送路断面 | 小 | 大 | 大 | 大 | 大 |
補修 | 容易、主にベンド | 比較的小 | 全面的 | 全面的 | バケツ,チェン |
輸送物の最高温度(℃) | 600 | 50 | 150 | 150 | 150 |
輸送物の最大粒径(mm) | 30 | とくになし | 50 | 50 | 50 |
最大輸送距離(m) | 2,000 | 8,000 | 150 | 50 | 50 |
設備費、労力費 | (一例としてアルミナ10t/hを500m輸送する場合の概算値)) | ||||
動力(kW) | 150 | 25 | 25 | ||
動力比較 | 100 | 16.7 | 16.7 | ||
概算金額(万円) | 2,000 | 5,400 | 5,400 | ||
金額比較 | 100 | 270 | 270 |
空気輸送搬送装置の種類と特長
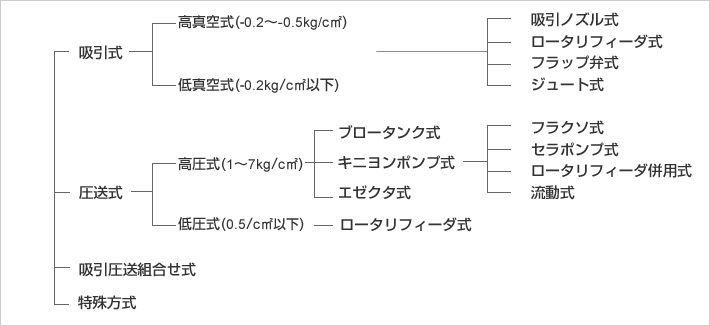
空気輸送搬送装置の種類と特長
空気輸送搬送装置にはいろいろな種類や方式がありますが、輸送条件にたいして適切な方式と機器を選定し、その仕様と空気源機械の容量を過不足なくきめることが必要です。 なお、空気輸送搬送装置の一般的な特長はつぎのとおりです。
- 輸送物の包装,解袋が不要で、作業能率が大きく、また経費が節減される。
- 設備が簡単で据付け面積が小さく、設備費、修理費が少ない。
- 運転要員は輸送量にかかわらず、少人数ですみ、全自動無人運転も行なうこともできます。したがって、人件費が少なくてすみます。
- 輸送経路を比較的任意にとることができ、工場の設備配置を合理化することができます。
- 天候や管路周辺の条件に無関係に輸送することができ,生産工程の計画がたてやすくなります。
- 輸送物の吸湿、汚損、あるいは異物の混入をさけることができ、品質の保持と衛生上このましい状態を作れます。
- 輸送中に混合、粉砕、分級、乾燥、冷却、除じんなどの操作も行なうことができます。
- 長い距離の集約、あるいは分散輸送が可能になります。
- 化学的に不安定な粉粒体も特殊なガスを用いて安全に輸送することができます。
- 低圧あるいは高圧の容器内へも供給、輸送することができます。
それぞれの用途と諸条件に適応するように空気輸送搬送装置にはいろいろの方式と機器の種類があり、食品工業、化学工業、石油工業、窯業、製紙工業、鉱業、鉄鋼工業、ボイラ灰処理など各方面で広く用いられています。
これらの長所の反面、他の機械的輸送装置に比べて、一般に所要動力が多いこと,輸送できる粒子の大きさが約50mm以下に制限されること、粘着性の強いものには不向きなこと、などの短所もあります。
所要動力だけについては不利であっても、工場設備の都合から空気輸送搬送の長所を利用したい場合や、その特長を発揮して品質や生産性を高めたい場合が多く、いろいろな方面に空気輸送搬送が採用されています。
また、新らしい方式の空気輸送搬送装置が考案され、従来の方式の短所とされていた点が格段に改良され、輸送の合理化と生産性に寄与しています。
大気を吸引して輸送管中に気流を作り、これに粉粒体を供給して気流とともに輸送する方式で、一般的に、
- 供給器,吸引ノズル → 輸送管
- 分離捕集器 → 抽気機
からなっています。この方式の一般的な特長はつぎのとおりです。
- 数個所から1個所へ集約輸送する場合に適している。
- 広い場所に山積,あるいは低いところ、深いところにある粉粒体を輸送する場合に適している。
- 貯蔵タンク下やホッパの下が狭くて、圧送式では供給器が設置できない場合も輸送することができる。
- 輸送の始点で粉粒体の飛故を避けたい場合に適している。
- 輸送の始点で、その上部のタンク、ホッパヘ空気の漏れを避けたい場合に適している。
- 粉粒体の投入口は開放のままでよく、連続的に追加投入して輸送をつづけることができる。
- タンク、ホッパから落下しにくい粉粒休でも圧送式に比べて円滑に供給し、輸送をつづけることができる。
- 供給器の構造が圧送式の場合よりも簡単になる。
- 粉粒体中に空気源機械の油分やドレンが混入することがない。
- 輸送経路中は大気圧以下になるため、装置に間げきがあっても粉粒体が漏れることとがない。
- 粉粒体は大気圧以下の気流によって扱われるため水分が蒸発しやすく、水分の多い粉粒休も圧送式に比べて輸送しやすい。
- 圧送式に比べて分離捕集器の構造が複雑になる。(気密を保ちながら粉粒体を排出する必要がある)
- 圧送式に比べて輸送量、あるいは輸送距離が制約される.(大容量あるいは最距離の輸送には不向きである)
- 吸引式には低真空式と高真空式とがありますが、前者には一般集じん装置,工場内の小容量輸送装置などが、後者には容量の大きい集じん装置、化学工場や食品工業の輸送装置、船あるいは貨車からの荷揚装置、火力発電所の灰処理装置などがあります。
抽気機は、抽気量と真空度に応じてファン、ブロワ、ルーツブロワ、液封形真空ポンプ、往復動形真空ポンプ、エゼクタなどを用います。
吸引式の供給器
輸送管に粉粒体を供給する供給器には開閉ダンパ、フラップ弁、ロータリフィーダあるいは吸引ノズルなどを用います。
すなわちサイロ下やホッパ下から麦、大豆などの穀類あるいは落下しやすい粒体を吸引輸送する、簡単な装置では落下口を一定の開度に開く、ダンパで開閉して輸送と停止を制御することが多いです。
また大きな容量の輸送装置あるいは混合比を高めてできるだけ能率をあげるように計画してある装置では閉そくを避け、円滑に輸送するために粉粒体を定量的に供給する必要があるのでロータリフィーダを用います。
灰処理装置などのように硬い粉体や付着性のある粉体、あるいは温度の高い粉粒休を供給する場合にはフラップ弁を用い、輸送圧力を検知して自動的に開きの程度を制御することが多い。
船のハッチや貨車、あるいは深いところや広いところに山積みされた粉粒体を吸引輸送するには、供給器として吸引ノズルを用います。
ダンパやロータリフィーダは圧送式でも用いますが、吸引ノズルは吸引方式にだけ用いる独得の供給器ということができます。
吸引ノズル
吸引ノズルは外気とともに粉粒体を吸込んで輸送管中に供給するもので、その優劣がこの方式の装置の性能にいちじるしく影響します。
吸止ノズルが持つべき一般的な性能上の条件はつぎのとおりです。
- 一定の吸引空気量にたいして,最小の圧力損失で最大の吸引量をもつ。
- 連続的に定量吸引ができる。
- 吸引する粒子の破砕が極小であること一一気流および粒子の速度、および方向に急激な変化がなく、粒子の加速が円滑に行なわれること。
- 操作が容易なこと。
- 任意に吸引状態を調節加減できること。
- 構造が簡単で耐久性があること。
一般に吸引方式では吸引圧カ-5000mm Aq程度の抽気機を用いるが、吸引ノズルにおける圧力損失は装置全体の圧力損失中かなり高い割合いを占めるので、できるだけ圧力損失の少ない形式の吸引ノズルを用いて、輸送に許される圧力の大きさを増すことがこの方式の装置の計画の1つの要点になります。
圧送式空気輸送搬送装置
圧送式の特長
輸送管中に空気を吹き流して、これに粉粒体を混充輸送する方式で、一般的に
空気源機械 → 供給機 → 輸送管 → 分離捕集器
からなっています。
この方式にはいろいろな形式のものがあるが、一般的につぎのような特長を持っています。
- 1個所から数個所へ分散輸送する場合に適する。
- 大容量の粉粒体を長距離に輸送する場合に適する。
- 輸送空気の圧力上昇は空気源機械の最高吐出圧力までゆるすことができるので、輸送条件が多少変っても,ある程度の順応性を持っている。
- 大気圧以上の圧力を持つ容器内へも供給愉送することができる。
- 機器,輸送管内は大気圧以上になるので、機器の接続部に聞けきがあつても、外気や雨水が侵入することがない。
- 分離捕集器の柑造が簡単になる。
- 供給器の構造が複雑になる(気密を保ちながら輸送物を供給する必要がある。
- 輸送圧力が高い場合は、供給器上部のタンク、ホッパを密閉構造にする必要があり、輸送は間けつ的になる。
圧送式には低圧式と、高圧式とがあり、前者は比較的小容量、短距離輸送の場合に、後者は大容量、長距離輸送の場合に相当します。
空気源機械は要求される空気量と圧力に応じてブロワ、ルーツブロワ、往復動形空気圧縮機などを用います。
一般に短距離の輸送では、比較的多量の空気を用いて太い管で輸送する低圧式が、長距離の輸送では少ない空気で細い管による高圧式が有利です。
吸引式においてもいえることであるが、とくに圧送式の場合は供給器の選択を慎重にして、輸送の条件に適合した方式の供給器を選定することが重要です。
供給器の選定にあたっては装置全体の運転条件に適合した方式であることはもちろんのこと、輸送物の性状、輸送量,使用場所の圧力、温度、水分などに注意して選定を誤らないようにすることが必要になります。
選定を誤ると装置が所期の性能を発揮しないばかりでなく、設備の運転に支障をきたすといっても過言ではありません。
なお供給器単体としてはつぎの諸条件を満足することがのぞましいでしょう。
- 粉粒体を一定量ずつ供給すること
- 粉粒体を加速しやすい状態で供給すること
- 粉粒体粒子を粉砕しないこと
- 粉粒休および空気のもれがないこと
- 所要動力が少ないこと
- 磨耗が少なく、耐久性があること
- 部品の取替修理が容易なこと
- 据付面積が小さいこと
- 据付高さが低いこと
- 取扱いが容易なこと
- 供給量の変更が可能で容易なこと
これらの諸条件をすべて同時に満足することはとうてい不可能で、それぞれの場合に応じて要求される性質のうち重要なものをできるだけ満足し、他はさしつかえない程度に軽視するなど、状況に即した計画が必要になります。
供給器には様々な方式がありますが、一般に用いられている代表的なものは、次の通りです。
- ロータリフィーダ
- スクリュフィーダ
- フラップフィーダ
- テーブルフィーダ
- チェンフイーダ
- バイブレーティングフィーダ
- ゲートフィーダ
- ブロータンク(フラクソ式、セラポンブ、流動タンク、圧送タンク)
- エゼクタフイーダ
これらの供給器の種類に応じて輸送装置の機器,構造、全体の設備内容が異なってきます。
以下にそれらのうち代表的なものについて概説します。
ロータリフイーダ式空気輸送搬送装置
特徴
ケースの内で回転するロータの羽根の間に粉粒体を供給し、これを輸送管に供給するものです。
様々な構造のものがあるが、一般的に次のような特長を持っています。
- 大きさが小さく、狭いところや低いところにも容易に取付けられる
- ほぼ定量的に供給することができる
- 回転数を変えることによって容易に供給量を変えることができる
- 粉休でも粒体でも扱うことができる
- ある程度の気密を保つことができる
- 約300℃までの高温物も扱うことができる
- 構造が簡単で保守、運転が容易である
- 分解修理が容易である
粉粒体は回転する羽根によって供給されるので、ほぼ定量的に落下供給できることが大きい特長で、輸送管中で定常的に均―に近い状態で粉粒体を輸送するためにこのましい供給器です。
運転は多くの場合、ギャードモータの回転をチェンによってスプロケットホイールに伝えて行ないますが、スプロケットホイールの大きさを変えることによってロータリフィーグの回転数、すなわち供給量を容易に変えられることも好都合な特長です。
したがって運転状態に応じて容易に輸送量の変更,調整を行なうことができます。
ロータリフィーダ
ロータリフィーダは取扱う粉粒体の性状(種類、粒度、比重量、温度、付着性、摩粍性、腐食性、溶融度など),圧力の程度,ゆるされる錆の程度,製作の難易と個数などをあわせ考慮して、構造と材質を選定します。
これらの諸条件に適合して、それぞれの場合にたいして計画することが必要です。
ロータリフィーダは比較的簡単な原理と単純な構造のものであるだけに、それぞれの場合に応した計画の適否カや性能と耐久性、運転管理の手数にいちじるしく影響します。
構造的には使用目的に応じてつぎのようなものがあります。
- テーパラズ式
- 吹上げ防止構造
- かみ込み防止構造
- 微粉排せつ構造
- 連続供給構造
- エゼクタ付構造
- 過負荷防止構造
低圧圧送式
ロータリフィーダのケースとロータとの間には、わずかではあるもののギャップが設けられているため、輸送圧力の程度に応じて輸送用空気が吹き上ります。
輸送圧力が比較的低い場合や大きい粒子、あるいは比重量の大きい粉粒体を扱う場合は、吹上げる空気の影響は少なく、また多少吹上げがあっても上記の防止装置によって粉粒体の落下不良によるトラブルを生じないように処理することができ、上部のホッパは大気に開放のままで連続的に粉粒体を供給輸送できます。
工場内の小容量あるいは短距離輸送ではルーツブロワを空気源機械としてこの方式による輸送が多いようです。
高圧圧送式
輸送圧力が高い場合や軽い粉粒体を扱う場合は吹上する空気によって落下不良をきたし、ひどい場合は輸送自体ができなくなってしまいます。
このためにホッパを密閉構造として粉粒体を受け入れた後に密閉し、空気の吹上げによる落下不良を避けなければなりません。
このために輸送はホッパー杯ごとのバッチ輸送になります。
比較的大容量の粉粒体を長距離に輸送する場合は輸送圧力が高くなるため、後者の方法をとることが多いようです。
キニヨン式空気輸送搬送装置
キニヨンポンプともよばれ、セメントや粉炭の輸送に多く使用されている圧送式空気輸送搬送機の1種です。
機構はスクリューポンプにより粉体を送り固めて、気密層を作りながらノズル室に送り込み、ついでノズルから噴射する圧縮空気により、粉体を輸送管内に吹き飛ばして輸送するものです。
輸送用空気以外に、スクリュを駆動するための動力が必要であるから、全消費動力は後述のブロータンク式に比べて相当多くなります。
しかし頑丈であるとともに,小柄である長所を持っているので上記のような特殊な用途に用いられています。
なおスクリュは一般|こ摩耗がはなはだしく、耐摩耗金属で作っても数ヵ月ごとに交換修理が必要になります。
プロータンク式空気輸送搬送装置
容器内に粉体を受入れて密閉後、圧縮空気を吸込んでこれを吐出管から輸送管内に噴出させて輸送するものです。
用途に応じていろいろな形式のものがあります。
容器内に粉体を受入れる方法には、真空作用を利用して吸込ませるものと、粉体の自重で落ち込ませるものとの2種類があります。
また、吐出管が本体から斜め上方向に出ているフラクソ式と、斜め下方向に出ているセラポンプ式とがあります。
それぞれ本体のタンクが1個で受入れと圧送を繰返す単胴形と、左右2個のタンクで交互に受入れと圧送を繰返す双胴形とがあります。
特徴
ブロータンク式にはつぎのような独得の特長があります。
消費動力が少ないタンクに受入れた粉体を圧縮空気にまり噴出して輸送する方式であるため、高混合比の輸送が可能であり、単位輸送量当りの消費動力が少なくなります。
大容量、長距離の輸送に適する粉体を本体内に入れて密閉してから輸送用の圧縮空気を吹込むので漏れの心配がなく、かつ輸送圧力は空気源機械の最高吐出圧力までゆるすことができます。
従って、高能率の大容量、長距離の輸送が可能になります。
本体内に一定量の粉体を受入れて圧送を行なうので、本体があたかも枡のような役目をします。
従って、別にカウンタゲージを取りつけ、送出弁に連動させて圧送回数を計測すれば、総輸送量を自動的に算出することができます。
補修はときどきバルブシートを交換するだけで十分で、予備品としてはバルブシートおよび充満検知用の水銀スイッチを要する程度ですみます。
騒音が少ない本体上部に取付けた満杯検知用の200ワット電動機が静かに回るほかは可動部分がないのできわめて静かです。
全自動運転が可能である粉体の満杯検知器、リミットスイッチ、電磁弁、圧カスイッチ、ダイヤフラム弁などを用いて全百動連続運転することができ、まったく人手がかかりません。
またその運転の状態は制御箱に取付けてあるパイロットランプ、圧力計によって容易に知ることができます。
この方式は上記のように多くの長所を持っていますが、セメントやフライアッシュなどの流動しやすいワークに限られます。
標準的な仕様
この方式の輸送装置の輸送能力は輸送物の性状と輸送管の内径と距離、使用する空気量によって決まることはもとより、本体の大きさと構造、本体内部における粉休の流動化状態、さらに輸送管の配管状態にも関係します。
従って、配管の経路、ベンドの曲率半径などの選択を慎重に行って輸送抵抗が小さくなるようにする方が良いでしょう。
流動形ブロータンク式空気輸送搬送装置
構造・特徴
プロータンク式の1種ですが、本体の内面に多孔板を取付け1本体内の粉体の流動攪拌をよくすることにより輸送能力の向上を計ったものです。
この方式には横形とたて形とがあり、ともにつぎの特長があります。
- 本体内の粉体の流動攪拌がよく行なわれるため、低い速度で輸送することができ、輸送圧力が従来のプロータンク式よりも小さく,機器の構造が簡単になる。
- 使用空気量が少なく、輸送圧力が低いため、空気源機械の容量と所要動力が小さくてすむ。
- 従来のブロータンク式よりもはるかに高い温合比で能率的に粉体を輸送することができる。
- 輸送速度が小さいので、輸送管や切換弁の摩耗,損傷が少ない。
- 横形は据付高さが低くてすみ、たて形は据付面積が小さくてすむ。
- プロータンク式と同じく運転は制御装置によって全自動化することも遠隔手動にすることもでき,運転操作が容易である。
粉粒体輸送関連資料
各種材料と輸送装置の適否
材料 | フライトコンベア | エプロンコンベア | 鋼製スクリュー | 鋳鉄 スクリュー |
連続 流動 |
ベルト コンベア |
吊下げ バケット |
スキップ ホイスト |
空気 コンベア |
低速 バケット エレベータ |
高速 バケット エレベータ |
振動 コンベア |
---|---|---|---|---|---|---|---|---|---|---|---|---|
灰(湿) | a | d | + | d | d | + | + | + | ||||
灰(乾) | a | d | + | + | d | d | + | + | + | + | ||
セメント | + | + | + | b | + | + | + | h | ||||
薬品 | ||||||||||||
磨耗性 | a | + | + | + | + | + | + | + | + | |||
腐食性 | + | + | + | + | + | + | + | |||||
粘着性 | + | |||||||||||
粘土 | + | + | + | + | h | + | d | d | + | + | + | |
石炭 | + | + | + | + | + | l | + | + | + | + | + | + |
コークス | + | + | e | + | + | + | f | + | ||||
フライアッシュ | d | + | + | + | d | + | d | + | + | |||
穀物 | d | + | + | + | f | + | ||||||
重鉱石 | + | + | + | + | + | + | + | |||||
軽鉱石 | + | + | + | + | g | + | + | + | + | + | + | |
食塩 | + | + | + | + | + | d | d | + | + | + | d | |
砂 | d | d | + | + | d | + | + | h | ||||
鋸屑 | d | d | + | + | + | d | + | + | ||||
泥状物 | c | + | ||||||||||
ソーダ灰 | + | d | + | + | + | + | d | + | + | + | ||
デンプン | + | + | + | f | + | + | ||||||
砂糖 | d | + | + | + | f | + | + | |||||
高温材料 | + | + | + | + |
(注)+:適 、a:チェーンコンベアのみ、b:粉塵飛散の防止、C:リボン型が最良、d:可能であるが一般的ではない、a:赤熱状のものは不可、f:乱暴に取り扱わないこと、g:極度の摩擦性のものをのぞく、h:障害発生のおそれあり
供給物の性状よりみた供給機の代表型式とその選定表
分類 | 供給機名 | 輸送物の特性に対する適否 | 使用距離 | 使用型式 | 供給雰囲気(圧力) | 使用方法 | |||||||||||||||||||
---|---|---|---|---|---|---|---|---|---|---|---|---|---|---|---|---|---|---|---|---|---|---|---|---|---|
型 | 型式 | 供給状態 | 粉体 | 粒体 | 中塊 | 磨耗 | 腐食 | 付着 | 浮遊 | 高温 | 直接 | 近距離 | 中距離 | 遠距離 | バッチ式 | 連続式 | 大気圧以下 | 大気圧 | 低圧 | 中圧 | 高圧 | 単独 | 他と組合 | ||
面積型 | 単一式 | 開放型 | 重力流動 | 差込ダンバ | ○ | △ | ○ | △ | ○ | ○ | ○ | ○ | ○ | ○ | ○ | ||||||||||
密閉型 | スライダダンバ | ○ | △ | △ | ○ | △ | ○ | ○ | ○ | ○ | ○ | ○ | ○ | ○ | |||||||||||
ブラストゲートバルブ | ○ | △ | ○ | △ | ○ | ○ | ○ | ○ | ○ | ○ | ○ | ○ | |||||||||||||
容積型 | 単一式 | 開放型 | ホッパ | ○ | ○ | ○ | ○ | △ | ○ | ○ | ○ | ○ | ○ | ○ | ○ | ||||||||||
密閉型 | 2重弁式供給機 | ○ | △ | △ | △ | ○ | ○ | ○ | ○ | ○ | ○ | ○ | ○ | ||||||||||||
強制流動 | ブロータンク式供給機 | ○ | △ | △ | △ | ○ | ○ | ○ | ○ | ○ | ○ | ○ | ○ | ||||||||||||
2重タンク式供給機 | ○ | △ | △ | ○ | ○ | ○ | ○ | ○ | ○ | ○ | |||||||||||||||
連続式 | 開放型 | 引きずり | チェンフィーダ | ○ | ○ | △ | △ | ○ | ○ | ○ | ○ | ○ | |||||||||||||
押し出し | スクリューフィーダ | ○ | ○ | △ | △ | △ | ○ | ○ | ○ | ○ | ○ | ○ | |||||||||||||
重力流動 | ターンテーブルフィーダ | ○ | ○ | ○ | ○ | △ | △ | ○ | ○ | ○ | ○ | ||||||||||||||
密閉型 | 引きずり | フローコンペヤ | ○ | △ | △ | △ | ○ | △ | ○ | ○ | ○ | ○ | |||||||||||||
押し 出し |
キニヨンポンプ | ○ | △ | △ | ○ | ○ | ○ | ○ | ○ | ○ | |||||||||||||||
強制 | エアースライド | ○ | ○ | △ | ○ | △ | ○ | ○ | ○ | ○ | |||||||||||||||
運搬型 | ロールフィーダ | ○ | △ | △ | △ | ○ | ○ | ○ | ○ | ○ | ○ | ||||||||||||||
ベルトコンペヤ | △ | ○ | ○ | △ | △ | △ | ○ | ○ | ○ | ○ | ○ | ||||||||||||||
ロータリーフィーダ | ○ | △ | △ | △ | △ | ○ | ○ | ○ | ○ | ○ | ○ | ○ | ○ | ○ | |||||||||||
バケットエレベータ | △ | ○ | △ | ○ | △ | △ | ○ | ○ | ○ | ○ | ○ | ||||||||||||||
振動型 | 連続式 | 強制 | 振動フィーダ | ○ | ○ | ○ | ○ | △ | ○ | ○ | ○ | ○ | ○ | ○ | |||||||||||
電磁パイブレータ | ○ | ○ | ○ | ○ | △ | ○ | ○ | ○ | ○ | ○ | ○ | ||||||||||||||
往復運動板型 | ○ | ○ | △ | △ | ○ | ○ | ○ | ○ | ○ | ||||||||||||||||
重量型 | 単一式 | 開放lW | ホンパスケール | △ | ○ | ○ | ○ | △ | ○ | ○ | ○ | ○ | ○ | ||||||||||||
密閉型 | タンクロードセル | ○ | ○ | ○ | △ | ○ | △ | ○ | ○ | ○ | ○ | ||||||||||||||
連続式 | 開放型 | ベルトスケール | △ | ○ | ○ | △ | △ | ○ | ○ | ○ | ○ | ||||||||||||||
その他 | インゼクタ | ○ | △ | ○ | ○ | ○ | ○ | ○ |
空気輸送搬送の対象となる粉体の諸性質
名称 | 平均粒径 (mm) |
真比重 | 見掛比重 | 浮遊速度 (m/s) |
輸送空気速度 (m/s) |
---|---|---|---|---|---|
小麦 | 長径 5~8 | 1.3~1.4 | 0.66~0.83 | 9.8 | 18~30 |
大麦 | 1.30~ 1.35 | 0.55~0.65 | 8.7 | ||
麦芽 | 0.5 | 8.1 | 21 | ||
玄米 | 長径 5~6.9 | 1.12~1.22 | 0.56 | 7.7~ 9.0 | 15~25 |
大豆 | 長径 3.5~10 | 1.18~1.22 | 0.52~0.75 | 10.0 | 18~30 |
落花生 | 0.3~0.4 | 12.5~15.0 | 15 | ||
玉蜀黍 | 0.7~0.75 | 8.9~9.5 | 30 | ||
菜種 | 1.53 | 1.22 | 0.73 | 8.2 | |
綿実 | 1.06 | 0.60 | 9.5 | ||
砂 | 35~150mesh | 2.6 | 1.41 | 0.4~1.8 | 30~45 |
褐炭(粒) | 0.75 | 8.7 | 20~30 | ||
褐炭(小塊) | 1.16~1.34 | 0.62~0.8 | 10.6~11.0 | 18~40 | |
セメント | 0.018以下 | 3.10~3.15 | 1.4~1.5 | ||
消石灰 | 65mesh | 2.0 | 0.4~0.5 | 30 | |
塩化ビニル | 15mesh | 1.3~2.5 | 0.63 | 0.48~ | |
硫安 | 20~60mesh | 1.77 | 1.0 | 25 | |
石灰窒素 | 2.0 | 1.12 | 20~30 | ||
閃亜鉛鉱 | 4.3 | 2.28 | 17.7 | ||
アルミ粉 | 100~150mesh | 0.8 | |||
フライアッシュ | 10~30π | 2.0~2.2 | 1.0~1.6 | 0.01~0.1 | 20~25 |
空気輸送搬送装置の方式と種類
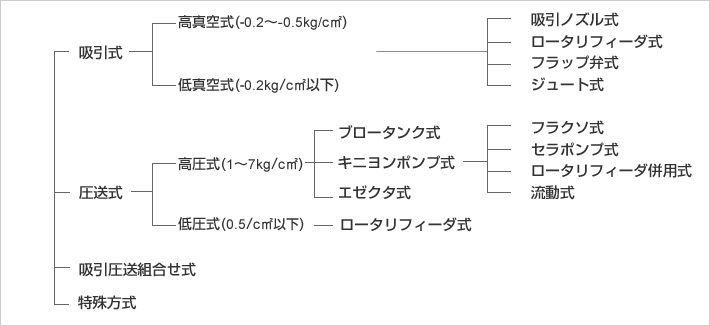